Epoxy paste grouting compound
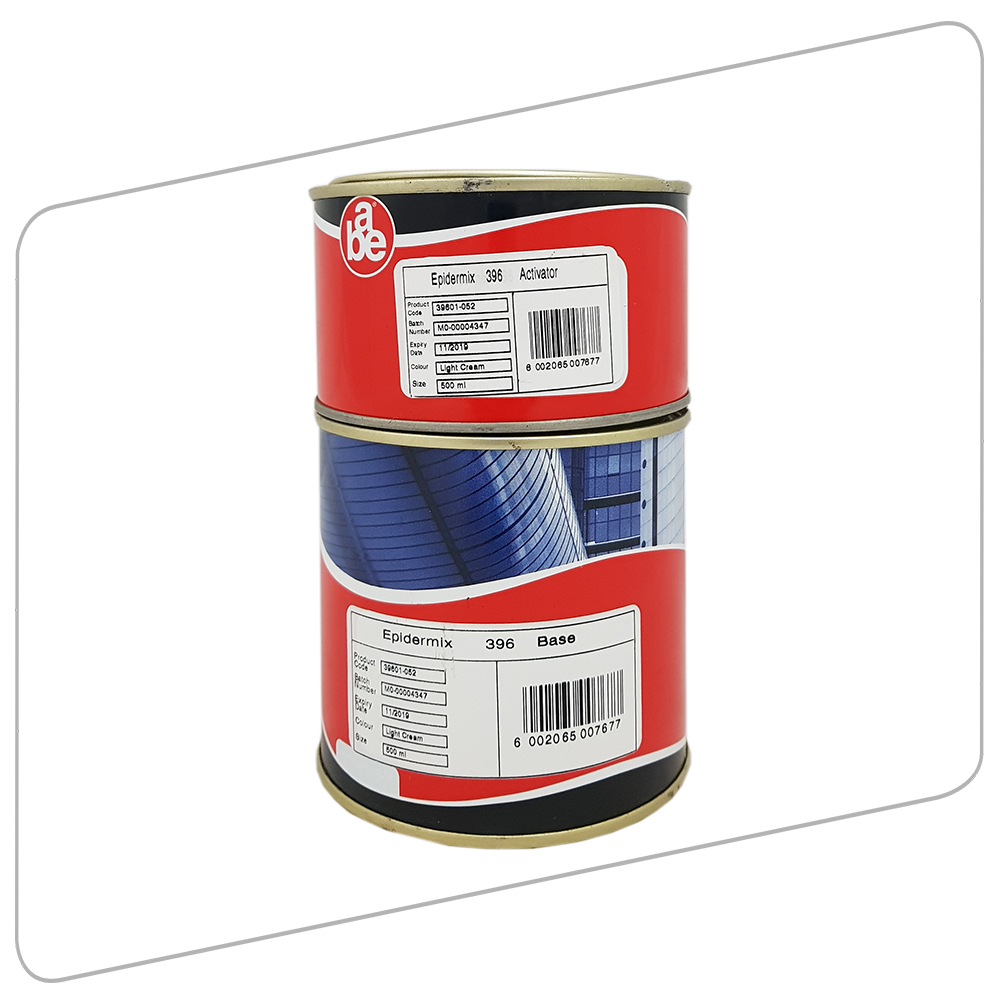
Two-component, thixotropic modified epoxy paste.
Uses:
As a grouting medium, either as supplied or converted into a mortar, for fixing dowel bars, bolts or other steel overhead or horizontally into concrete or rock. As a fast-setting non-flow adhesive. Grouting vertically downwards use epidermix® 396.
Advantages
- Will not drain from hole, including overhead
- Stronger than surrounding concrete and steel
Properties of Wet Material
Mixing ratio | Do not split kit |
Density | 1.14 g/cm3 |
Colour: Base Activator Mixed | White Dark Amber Light cream |
Flash point | > 100 °C |
Dilution | Do not dilute |
Consistency | Thixotropic paste |
Shelf life | 2 years from date of manufacture |
Storage conditions | Store under cover in cool place |
Packaging | 500ml |
Fire resistance | Non flammable |
Surface Preparation
All surfaces must be clean, sound and dry.
Cast concrete must be free of all laitance, dust and foreign matter. Drilled concrete must be free of dust and debris and if wet-drilled must be dry and free of all traces of slurry. Any glaze caused by core drilling must be removed by mechanical roughening to ensure good bonding between the adhesive and the concrete rock surface. Close-fitting burrs attached to a long shaft mounted in a power drill will aid in this respect. Smooth steel should be abrasive blast cleaned and must be free of scale, rust and oily material. Deformed and threaded bars should be oil and grease free and preferably free of rust and scale.
Bonding / Priming
Self priming.
Mixing
Mix both containers individually and ideally use a can opener to remove the lip of the containers. Transfer complete contents of both containers to a large clean board or plate, setting up the components side by side and not one on top of the other. Do not combine the components until other aspects of the job are ready. When ready to mix, combine the ingredients together and blend, using at least two trowels or spatula, until the compound is completely mixed. If a mortar is required, add an equivalent volume of silica grit and continue mixing until a homogeneous material is obtained.
Properties of Cured Material
Maximum service temp | 70°C |
Compressive strength @ 25 °C | 90 MPa @ 7 days |
Solvent resistance | Resists: aliphatic solvents, vegetable and mineral oils and greases, petroleum fuels |
Water resistance | Excellent |
Tensile strength @ 25 °C | 21 MPa @ 7 days |
Toxicity | Non-toxic |
Coverage
Grouting with epidermix® 396 – Quantity Calculations:
The quantity of grouting material can be calculated from the formula:
0,8 (D + d) (D – d)HN = liters of grout required
1000
where:
D = diameter of hole in cm
d = diameter of bar in cm
H = depth of hole in cm
N = number of holes
If the dimensions are taken in centimeters, dividing the answer by 1 000 will give the number of liters of grout required, at a 2:1 filling ratio, half of this volume of epidermix® will be needed. At 1:1 filling ratio, three quarters of this volume of epidermix® will be needed. These figures make no allowance for site wastage of material.
Provided deformed or threaded steel, either mild or high tensile, is embedded at least 15 diameters it can be expected that any failure of the assembly will be due to tensile rupture of the steel. Thus epidermix® grouting allows the steel to develop its full design strength. Regarding the ratio of hole to rod diameter it has been shown that the ultimate coverage bond stress is at its highest at a ratio of 1,3. This reduces as the ratio increased to 1,67 thereafter remaining constant. By increasing the ratio from 1,3 to 1,5 the ultimate average bond stress is decreased some 15%. At a ratio of 1,67 the ultimate average bond stress has decreased some 20%.
Application
If grouting horizontally or overhead, a mastic gun is required with a length of plastic tubing of sufficient diameter to fit tightly over the gun’s nozzle. The tube must be long enough to reach the back of the hole.
Fill the gun with the mixed epoxy compound or mortar and pump material into the back of the hole, slowly withdrawing the tube until sufficient material has been deposited to fill the hole once the bar has been introduced.
The bar should be introduced with a rotary motion to ensure wetting of both bar and concrete, if it is important that the bar is truly horizontal a jig or template must be used until the com-pound has set.
Properties During Application
Application by | Trowel or mastic gun |
Volume solids | 100% |
Pot life | 15 °C | 20 °C | 25 °C | 30 °C | 35 °C |
500ml | 80 min | 60 min | 40 min | 30 min | 20 min |
1L | 60 min | 45 min | 30 min | 22 min | 15 min |
Application temp range | 10°C to 40°C Temperature of metal to be grouted should not exceed 25°C at time of grouting. If application temperature is above 30°C consult. a.b.e®.’s Technical Department for special precautions |
Maximum application rate | Do not grout unfilled epidermix® 396 into a hole larger than 1,5 times bar diameter. When grouting with filled epidermix® 396 annulus width should be kept as small as possible. |
Application rate | If mixed, unfilled epidermix® 396 will be sufficient for: 1L annulus volume. 1 L mixed epidermix® 396 filled with dry silica grit will be sufficient for 1,3L annulus volume filled at a loading of 1:1. these figures do not allow for any wastage, which can run as high as 20 – 25%. |
Fire resistance | Non-flammable |
Equipment clean-up | abe® super brush cleaner |
Colour | Ligh |
Cleaning
lean with abe® super brush cleaner, before the epoxy has set, after which rinse well with clean water.
Protection on Completion
Against traffic and spillage until cured.
Temperature & Relative Humidity
See “Properties of wet material”, ”Cured material”, and “During application”.
Model Specification
Two component, low creep, structural epoxy paste grouting compound for fixing starter bars and bolts horizontally or vertically up.
The grouting compound shall be epidermix® 396, a two component, thixotropic structural epoxy compound applied in accordance with the manufacturers recommendations, a.b.e.®
Packaging
epidermix® 396 is supplied in 500ml metal containers.
Handling & Storage
This product has a shelf life of 24 months if kept in a dry cool place in the original packaging. In more extreme conditions this period might be shortened.
Health & Safety
Wet epidermix® 396 is toxic but non flammable. Always ventilate the working area well during application and drying. Always wear gloves and eye protection when working with the material and avoid excessive inhalation and skin contact. If material is splashed in the eye, wash with copious quantities of clean water and seek medical attention. Cured epidermix® 396 is inert and harmless.
When transporting liquids and semi liquids by aircraft, ask for material safety data sheet.
Important Notice
This data sheet is issued as a guide to the use of the product(s) concerned. Whilst a.b.e.® endeavours to ensure that any advice, recommendation, specification or information is accurate and correct, the company cannot accept any liability for application – because a.b.e.® has no direct or continuous control over where and how a.b.e.® products are applied.
Further Information
Where other products are to be used in conjunction with this material, the relevant technical data sheets should be consulted to determine total
requirements.
a.b.e.® has a wealth of technical and practical experience built up over the years in the company’s pursuit of excellence in building and construction
technology.