Epoxy adhesive, filler and grout
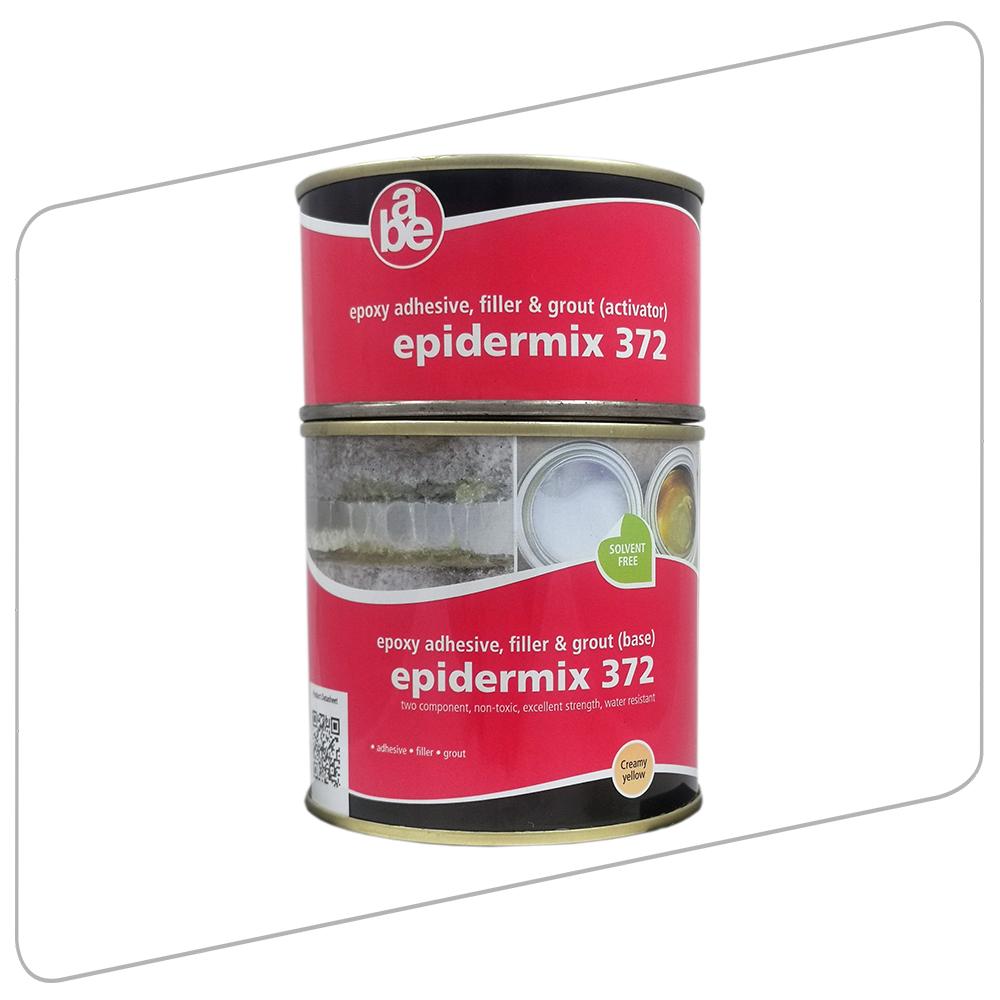
epidermix® 372 is a two-component, solvent-free, thixotropic, polyamide cured epoxy adhesive.
Uses:
As a general purpose adhesive for most materials, excluding certain plastics and stainless steel. If required in structural load bearing applications the a.b.e.®‘s Technical Department should be consulted and supplied with full details of the design.
As a filler where it may be bodied with fine materials such as wood flour, silica sand and talc, to match the material being filled.
As a grouting medium for fixing dowels and bolts, horizontally into concrete and rock.
Advantages
- Solvent-free
- Non-slump
- Easy to mix
- Bonds most materials
- Can be filled for use as a grout
- Economical
Surface Preparation
Any surface to be treated must be clean, sound and dry. It must be free of foreign matter such as oil, grease, paint, dust, debris of preparation and any other form of contamination. Smooth surfaces should be roughened by some appropriate method.
Preparation of specific surfaces:
- Cast concrete and pockets in concrete – free of all laitance and shutter release.
- Drilled concrete and rock – if wet drilled, free of all traces of dry slurry; if dry drilled, free of all drilling debris.
- Fibre cement – free of all dust.
- Smooth steel – free of millscale, rust and other foreign matter. Ideally abrasive blast cleaned.
- Deformed and threaded steel – free of oil, grease and rust.
- Aluminium – free of grease. Abrade and degrease. Bond immediately.
- Stainless steel – is not a candidate material.
- Timber – roughen by rasping. Oily woods (e.g. teak) should be acetone washed.
- Glass – detergent wash, clean water rinse, alcohol rinse.
- Glass fibre laminates – abrade to expose fibres and solvent wash.
- Ceramic (unglazed) – contamination free and dry.
- Stone – free of contamination.
- Rubbers – degrease and roughen.
- Thermoplastic plastics (except polystyrene) – are not candidate materials.
- Polystyrene – must be free of foreign matter.
Typical Physical Properties of Wet Material
Colour | Base: White Activator: Amber Mixed: Creamy-yellow |
Density | 1,15 g/cm3 |
Pot life (minutes) | 120 minutes @ 15 °C 90 minutes @ 20 °C 60 minutes @ 25 °C 45 minutes @ 30°C 30 minutes @ 35 °C |
Flashpoint | 120 °C |
Dilution | Do not dilute |
Consistency | 4 Thixotropic paste |
Typical Physical Properties During Application
Volume solids | 100% |
Curing time @ 25 °C | Touch dry: 6 hrs Practical use: 24 hrs Full cure: 7 days |
Sanding time @ 25 °C | If used as a filler requiring smoothing, sand after 24 hours cure |
Overcoating time @ 25 °C | Minimum: 12 hrs Maximum: 48 hrs if being over-coated with an epoxy system |
Fire resistance of wet material | Non-flammable |
Typical Physical Properties of Cured Material
Toxicity | Non-toxic |
Compressive strength @ 25 °C | 70 MPa |
Tensile strength @ 25 °C | ±30 MPa |
Maximum service temperature | Dry: 60 °C Wet: 40 °C |
Modified Arizona Shear test | 55 MPa prisms fail in concrete |
Grouting test at 15 diameter embedment | 12 mm HT bar fractured |
Lap shear (double overlap) strength on grit blasted steel | 16 MPa |
Shrinkage during cure | Negligible |
Water resistance | Excellent |
Solvent resistance | Resists aliphatic solvents, vegetable, mineral oils greases and petroleum fuels |
Bonding / Priming
No priming required.
Mixing
Mixing Ratio:
2 base to 1 activator by volume. Carry out mixing on a flat clean surface, such as a board or plate.
Set up carefully measured quantities (2 volumes base and 1 volume activator) of each component, side by side on the mixing plate. Do not mix until application site operations are ready. Use separate tools to remove each component from its container thus preventing contamination. With putty knives, paint scrapers or similar flat tools, mix the two components until a completely homogeneous material results. The larger the volume of the mix the longer should be the mixing time. If a filled material is required, add the filler only after complete mixing of the base and activator has been achieved. Remove mixed material to a clean surface and carry on mixing to ensure no unmixed material from the first mixing area is incorporated in the final product.
Coverage
Application rate:
- In general 1 litre of mixed epidermix® 372 covers 1 m2 to a thickness of 1 mm.
- As a grout 1 litre of mixed epidermix® 372 filled with an equal volume of abe®coarse No. 1 silica sand will yield approx. 1,3 litres of mortar.
Note: This information makes no allowance for site wastage.
Maximum application rate:
- AS AN ADHESIVE: Use thinnest possible film allowing for full wetting of adherents.
- AS A FILLER: Up to 15 mm thickness.
- AS A GROUT: Do not grout unfilled epidermix® 372 into a hole larger than 1,5 times the bar diameter. When grouting with filled epidermix® 372 the hole should be kept as small as possible.
Application
Application by putty knife, trowel or mastic gun.
As an Adhesive:
Mixed material should be spread onto the face of one adherent, thickly enough to extrude when both faces are mated. Bonded mating faces must be kept under compression until the adhesive layer has set. On heavy assemblies excess adhesive should be removed immediately and may be reused on other units. In delicate work such as jewellery bonding, extruded material should be left to obtain initial set and then cut off with a fine sharp blade. If prevention of staining of faces is important a release agent should be used, care being taken to see that it does not affect the mating faces.
As a Filler:
Mixed material should be smoothed into place using a trowel or similar tool. If filling requires feather edging, release agent may be applied to surrounding areas to preserve cleanliness. Use a mastic gun equipped with a length of tubing long enough to reach the back of the hole, which must be suitably vented. Once sufficient grout is in the hole, insert the bar using a rotary motion to ensure wetting all faces. Seal the mouth of the hole with a little very dry mortar grout to retain the epoxy grout during setting time.
Grouting With epidermix® 372:
Basis for strength calculations: Given adequate concrete strength and provided that a bar of deformed or threaded steel, either mild or high tensile, is embedded to a depth of at the least 15x the bar diameter, it can be expected that any failure of the assembly will be due to tensile rupture of the steel.
Thus epidermix® 372 grouting allows the steel and the concrete to operate at full design strength. Regarding the diameter ratio of hole to rod, it has been shown that the ultimate average bond stress is at its maximum at a ratio of 1,3:1. Ultimate average bond stress reduces as the hole:rod ratio increases to a value of 1,67:1. Thereafter it remains constant. An increase of diameter ratio from 1,3:1 to 1,67:1 will reduce bond stress.
Cleaning
Tools and mixing equipment should be cleaned immediately after use and before material has set with abe.® super brush cleaner followed by washing with soap and water.
Protection on Completion
If used as a filler and an epoxy coating is required allow a minimum of 12 hours and a maximum of 48 hours before commencing with epoxy coating.
Application Temperature
10°C to 40°C. If metal is being grouted, its surface should not exceed 25°C at the time of grouting.
Model Specification
General-purpose thixotropic epoxy adhesive.
The adhesive/grout will be epidermix® 372, a two-component, solvent-free, thixotropic, polyamide cured epoxy system applied in accordance with the recommendations of a.b.e.®. The compound will have a 7 day compressive strength of 70 MPa and a lap shear strength on grit blasted steel of 16 MPa.
Packaging
epidermix® 372 is supplied in 90 ml, 500 ml, 1 litre and 5 litre containers.
Handling & Storage
This product has a shelf life of 24 months if kept in a dry cool place in the original packaging. In more extreme conditions this period might be shortened.
Health & Safety
Wet epidermix® 372 is toxic but non-flammable. Ensure the working area is well ventilated during application and drying. Always wear gloves when working with the material and avoid excessive inhalation and skin contact. If material is splashed into the eye, wash with plenty of clean water and seek medical attention.
Cured epidermix® 372 is inert and harmless.
Important Note
This data sheet is issued as a guide to the use of the product(s) concerned. Whilst a.b.e.® endeavours to ensure that any advice, recommendation, specification or information is accurate and correct, the company cannot accept any liability for application – because a.b.e.® has no direct or continuous control over where and how a.b.e.® products are applied.
Further Information
Where other products are to be used in conjunction with this material, the relevant technical data sheets should be consulted to determine total
requirements.
a.b.e.® has a wealth of technical and practical experience built up over the years in the company’s pursuit of excellence in building and construction
technology.