Liquid (Non-Structural) Epoxy Adhesive.
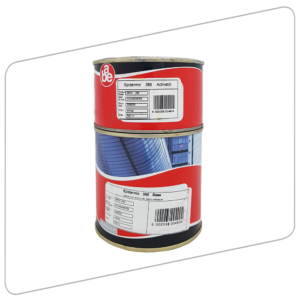
Two-component, solvent-free, polyamide cured epoxy.
General purpose liquid epoxy compound. Adhesive for various substrates. Binder for epoxy mortar. Crack injection compound. Coating for expanded polystyrene, primer for epoxy mortar, fibre glassing compound.
Advantages
- Solvent free
- Easily applied liquid
- Can be injected
- Mix with aggregates to form mortar
- Liquid general purpose adhesive
- Coating for polystyrene
Surface Preparation
Any surface to be treated must be clean, sound and dry.
It must be free of foreign matter such as grease, oil, old paint, dust, debris of preparation and any other form of contamination. Smooth surfaces should be roughened by some appropriate method. epidermix® 365 will not adhere to most thermoplastics and should also not be used to bond stainless steel, glass or non-ferrous metals.
Bonding / Priming
Self priming.
Properties of Wet Material
Mixing ratios | 1,5 base to 1 activator by volume |
Density (typical) | 1,04g/cm3 |
Colour: | Base: Pale Amber Activator: Dark amber Mixed: Amber translucent |
Flash point | + 120°C |
Dilution | Do not dilute |
Consistency | Medium viscosity liquid |
Mixed viscosity | 2800 cP |
Toxicity | Uncured material is toxic |
Shelf life | 2 years from date of manufacture |
Finish | Gloss |
Storage conditions | Store under cover in cool conditions |
Packaging | 500 ml, 5 l kits |
Properties During Application
Application by | Brush, short fiber roller, trowel for mortars, gun for crack injection |
Application temp | 10 °C to 40 °C |
Overcoating time @ 25 °C | Not less than 6 hours. Not more than 48 hours |
Curing time @ 25 °C | Touch dry – 12 hrs Practical cure – 24 hours Full cure – 7 days |
Volume solids | 100% |
Properties of Cured Material
Toxicity | Cured film non-toxic |
Max service temp. | Dry : 60 ºC Wet : 40 ºC |
Compressive strength @ 25 ºC | Unfilled : 75 MPa with 3 volumes silica filler : 100 MPa |
Tensile strength @ 25 ºC | Unfilled : 6,5 MPa with 3 volumes silica filler : 9 Mpa |
Lap shear strength on gritblasted steel | Unfilled : 9 MPa with 3 volumes silica filler : 4 Mpa |
Modules of rupture | Unfilled : 15MPa with 3 volumes silica filler : 27 MPa |
Modified Arizona shear test | Unfilled : 55 MPa prisms failed in concrete |
Grouting test 15 diameter embedment annulus 25% of diameter | 12mm HT bars fracture |
Shrinkage during cure | Negligible |
Creep : Where low creep is a design parameter epidermix® 365 should not be used. In such applications epidermix® 395 should be used. |
|
Solvent resistance | Resists aliphatic solvents |
Chemical resistance |
Dilute mineral acids limited resistance. Resists : 40% sodium hydroxide |
Pot Life (Minutes)
15ºC | 25ºC | 35ºC | |
500 ml kit | 150 | 105 | 70 |
Mixing
Stir each component separately and then add the activator to the base and stir with a flat paddle for at least FIVE MINUTES. It has been found that mechanical mixing gives better dispersion than manual mixing.
A suitable mixing method would be a slow speed electric drill (approximately 200 r/min) fitted with a paddle. If only part of a kit is to be used add 1 volume of activator to 1,5 volumes of base. Measuring must be accurate and separate stirrers and containers used for proportioning each component. If being used as a mortar binder combine base and activator as above and when fully mixed add in slowly, with agitation, up to 3 volumes dry, clean, abe® graded silica sand to give the consistency required. Under no circumstances exceed 3 volumes of silica. If impermeability is a prime requirement, fill in the range of 2,5:1.
Practical Coverage Rates
Adhesive | 1 – 4m2/ℓ (dependant on surface texture and porosity) |
Crack injection | 1 m2/ℓ in 1 mm wide crack |
Tile pointing mortar | 1 ℓ mixed epoxy liquid yields approx 3 ℓ mortar (when mixed 1:3 with abe® silica sand) |
Hold down bolt grout | 1 ℓ mixed epoxy liquid yields approx 1,9ℓ grout (when mixed 1:1,5 with abe® silica sand) |
Epoxy concrete | 1 ℓ mixed epoxy liquid yields approx 3,4 ℓ epoxy concrete (when mixed with 2 ℓ abe® graded silica sand and 2 ℓ 10 – 19mm washed and dried stone) |
When using epidermix® 365 as a grout, the hole diameter should be 1,3 – 1,5 times the diameter of the steel. When metal is being grouted, its surface temperature should not exceed 25 ºC at the time of grouting. |
Grouting – Quantity Calculations
The quantity of epidermix® 365 required may be calculated from the formula:
0,8 (D + d) (D – d)HN = litres required
1000
where D = diameter of hole (in cm)
d = diameter of metal (in cm)
H = depth of hole (in cm)
N = number of holes
This gives the total number of liters of grout required, without any allowance for wastage.
When a grout comprising of 1 volume epidermix® 365: 1,5 volumes of abe® silica sand is used, epidermix® 365 will comprise 60% of the final volumes. Diameter ratio of hole to rod should ideally be 1,3:1.
Safedeck System
Where used as a bonding coat in the safedeck system, the concrete surface should be primed with abecote® 386. This must be left overnight and then overcoated with epidermix® 365. The grit layer which provides the non-slip finish must be evenly broadcast into the wet epidermix® 365 at the rate of approximately 1 kg/m2.
This is left overnight and excess, loose grit swept off the following morning whereupon sealing with the selected top coat system may proceed. abecote® 320 or abecote® 441 are usually selected as the finish coat on safedeck systems. Always use abecote® 441 if the system is going to be exposed to ultra violet light.
Application
epidermix® 365 may be applied by brush or short fibre roller when it is used as a primer. Its resulting film must be overlaid with epoxy mortar while still wet or at least tacky. epidermix® 365 when used as an adhesive, should be applied by brush. The face of the one adherent should be lightly coated and all excess compound scraped off.
Apply a full coat of epidermix® 365 to the second adherent and sandwich the faces together maintaining necessary compression across the bond line. Remove all extruded material immediately and take care to pre-mask any areas which could be disfigured by excess adhesive. Strip masking as soon as adhesive flow ceases. epidermix® 365 mortar is normally trowelled into place onto a coat of still wet epidermix® 365 primer. Plastic wrapped shutters will be needed on vertical faces to retain the mortar until it sets.
Horizontal mortars may also need shuttering depending on the particular use of the material. If a very smooth open face is required work with a steel float moistened with white spirit to achieve the final polish. Details of crack injection procedures will be found in the relevant technical data sheet.
Cleaning
abe® super brush cleaner before dried/cured.
Protection on Completion
Against traffic ad spillage until cured. Most epoxies chalk and degrade in extensive sunlight.
Temperature & Relative Humidity
See “Properties of Cured and Wet Material.
Model Specification
Two-component, general-purpose liquid epoxy adhesive. Crack injection epoxy and tile pointing grout when mixed with blended silica sand.
The adhesive/grout shall be epidermix® 365, a two component, solvent free, polyamide cured epoxy system applied in accordance with the manufacturers recommendations, a.b.e.® .
The compound shall have a 7 day compressive strength of 75 MPa.
Packaging
epidermix® 365 is supplied in 500ml and 5 ℓ metal containers.
Handling & Storage
This product has a shelf life of 24 months if kept in a dry cool place in the original packaging. In more extreme conditions this period might be shortened.
Health & Safety
Uncured epidermix® 365 is toxic and flammable. Always ventilate a working area well during application and curing.
Avoid naked flames in the vicinity. Always wear gloves and eye protection when working with the material and avoid excessive inhalation and skin contact. If material is splashed in the eye, wash with copious quantities of clean water and seek medical advice.
Cured epidermix® 365 is inert and harmless.
When transporting liquids and semi liquids by aircraft, ask for material safety data sheet.
Important Note
This data sheet is issued as a guide to the use of the product(s) concerned. Whilst a.b.e.® endeavours to ensure that any advice, recommendation, specification or information is accurate and correct, the company cannot accept any liability for application – because a.b.e.® has no direct or continuous control over where and how a.b.e.® products are applied.
Further Information
Where other products are to be used in conjunction with this material, the relevant technical data sheets should be consulted to determine total requirements.
a.b.e.® has a wealth of technical and practical experience built up over the years in the company’s pursuit of excellence in building and construction technology.