Structural wet-to-dry concrete adhesive
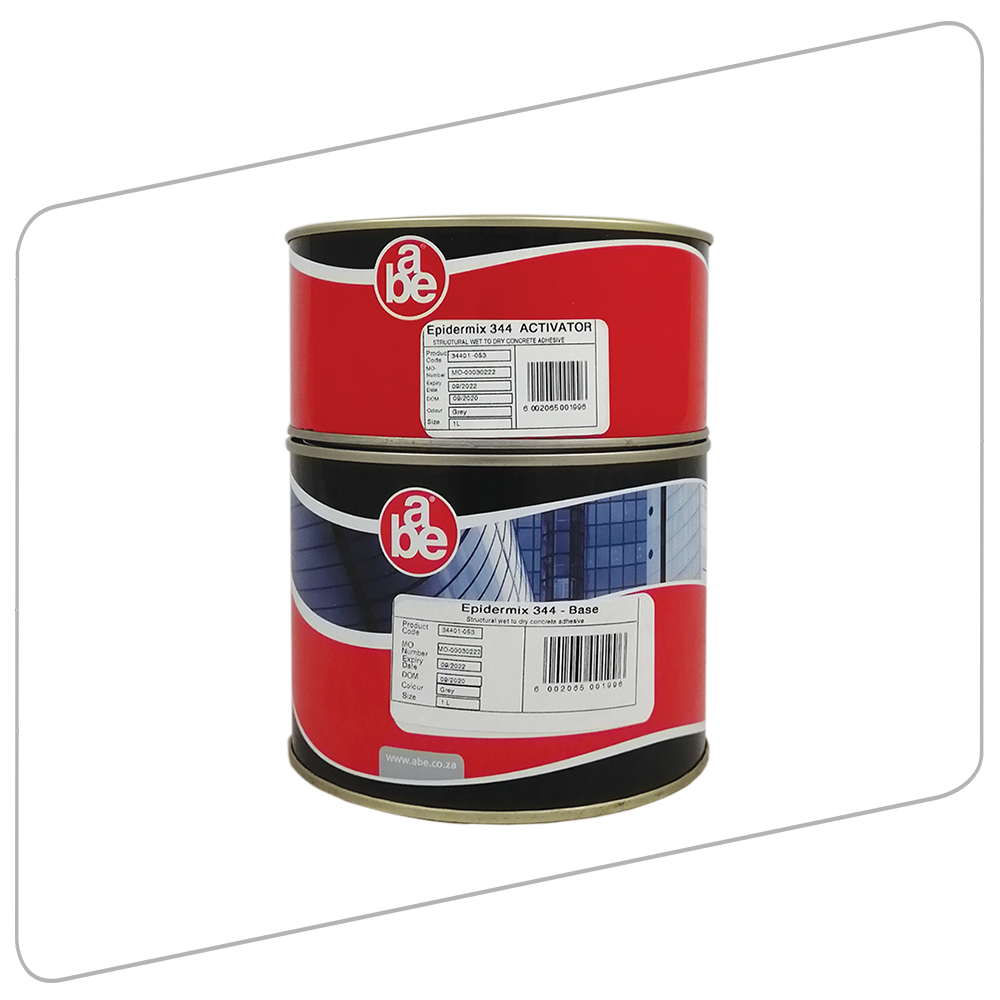
epidermix® 344 is a two-component, solvent-free, polysulphide modified epoxy adhesive.
Uses:
Bonding fresh (plastic) concrete to existing concrete, plaster to brickwork. Can be used to provide a damp-proof barrier within the concrete matrix. If applied onto reinforcing steel epidermix® 344 will cause no loss of concrete/steel bond strength.
Advantages
- May be used in structural situations
- Excellent bond to damp or dry surfaces
- High ultimate tensile strengths
- High ultimate lap sheer strengths
- Bonds to rock
Surface Preparation
The existing concrete surfaces must be clean and mechanically sound. They must be free of dust, laitance and any foreign matter as well as cracked or loose stone.
Maximum bond strength is only achieved if main aggregate of existing concrete is exposed. This may be done by scabbling, grinding, abrasive blasting or manual chipping. All cracked or loose aggregate must be removed.
In repairing spalls all loose and friable material must be broken away. If damage has exposed reinforcing, this should be undercut and hammered back into position, if so directed by the engineer. If exposed reinforcing has rusted badly it should be cleaned by abrasive blasting. The existing concrete surface should ideally be dry. epidermix® 344 will bond to green concrete. It will not, however, penetrate free water on the surface of any concrete.
Typical Physical Properties of Wet Material
Mixing ratio | 2 base : 1 activator by volume |
Density (mixed) | 1,66 g/cm3 |
Colour | Base: Black Activator: Off-white Mixed: Blue-grey |
Flash point | > 120ºC |
Dilution | Do not dilute |
Consistency | Semi-fluid paste |
Toxicity | Uncured material toxic |
Typical Physical Properties of Cured Film
Toxicity | Cured material is non-toxic |
Maximum service temperature | 90ºC |
Compressive strength | 100 MPa |
Tensile strength | 18 MPa |
Bond strength in concrete (ASTM C882-87) | Not <10,3 MPa after a 14 day moist cure period |
Steel/steel lap shear | 8 MPa |
Colour | Grey |
Pot Life (Minutes)
15ºC | 20ºC | 25ºC | 30ºC | 35ºC | |
500 ml kit | 60 | 45 | 30 | 18 | 15 |
1ℓ kit | 50 | 37 | 25 | 18 | 12 |
2ℓ kit | 40 | 30 | 20 | 15 | 10 |
Bonding / Priming
Self bonding.
Mixing
Stir well the contents of both containers individually and ideally use a can opener to remove the lip from both cans. Add the entire contents of the activator tin to the base material and stir with a flat paddle until an even, streak-free, grey mixture results. This takes at least five minutes.
If only a small quantity of material is required, pre-stir contents of each can using separate clean paddles. Remove two volumes of base and one volume of activator into a clean, separate container and mix together, to obtain an even grey colour. If the ambient temperature is between 10°C to 15°C pre-condition the unopened cans by standing them in the sun or in warm water until the temperature of the contents is approximately 20°C. This makes mixing and spreading much easier.
Coverage
1,7 – 2 m2/ℓ
Application
epidermix® 344 should be spread onto the surface as soon as possible after complete mixing. Apply the compound in a thin rough layer and only once the can is emptied should an attempt be made to spread to working thickness.
epidermix® 344 is best spread by means of a stiff bristle brush such as a kitchen scrubbing brush. A paint brush with bristles shortened by 50% may also be used.
On large areas use of a stiff-bristled yard broom is feasible. Compound should be spread at a rate of about 1,7 – 2 m2/ ℓ to give a film thickness of some 500 – 600 µm. Coverage is very much controlled by texture of the surface. The plastic concrete mix should be of as low a slump as feasible and may be cast into the adhesive layer up to 4 hours after mixing. If the original film has over-cured it must be roughened before application of the new layer of epoxy. Where a feather-edge is needed, the aggregate size of the concrete must be adjusted accordingly.
Vibration of New Concrete
Once the plastic concrete has been placed it should be punned with a steel or wooden rod to force main aggregate into the adhesive layer. When this has been done, vibration may be commenced. The vibrator head must be kept away from the adhesive layer. Poker vibrators have been found to give better results than vibrators clamped onto the shuttering.
Curing of New Concrete
Care must be taken to see that the new concrete is adequately cured as is required in good concreting practice. This curing is particularly vital where thin concrete layers are involved and should be continued for at least 5 – 7 days. See duracure range of curing agents.
Cleaning
Tools, brushes and mixing equipment should be cleaned immediately after use and before material has set with abe® super brush cleaner followed by washing with soap and water.
Protection on Completion
Not required.
Temperature & Relative Humidity
Application temperature range: 10°C to 40°C.
Model Specifications
Two-component, polysulphide modified epoxy compound for structural wet-to-dry concrete adhesive applications.
The adhesive will be epidermix® 344, a two-component, polysulphide modified, epoxy compound applied in accordance with the recommendations of a.b.e.®. The adhesive will have a bond shear strength of not less than 10,3 MPa in accordance with ASTM C882-87.
Packaging
epidermix® 344 is supplied in 500ml, 1ℓ and 2ℓ kits.
Handling & Storage
This product has a shelf life of 24 months if kept in a dry cool place in the original packaging. In more extreme conditions this period might be shortened.
Health & Safety
Wet epidermix® 344 is toxic and flammable. Ensure the working area is well ventilated during application and drying. Avoid flames in vicinity. Always wear gloves and eye protection when working with the material and avoid excessive inhalation and skin contact. If material is splashed into the eye, wash with plenty of clean water and seek medical attention.
Cured epidermix® 344 is inert and harmless.
Important Note
This data sheet is issued as a guide to the use of the product(s) concerned. Whilst a.b.e.® endeavours to ensure that any advice, recommendation, specification or information is accurate and correct, the company cannot accept any liability for application – because a.b.e.® has no direct or continuous control over where and how a.b.e.® products are applied.
Further Information
Where other products are to be used in conjunction with this material, the relevant technical data sheets should be consulted to determine total
requirements.
a.b.e.® has a wealth of technical and practical experience built up over the years in the company’s pursuit of excellence in building and construction
technology.