Flowable epoxy grout
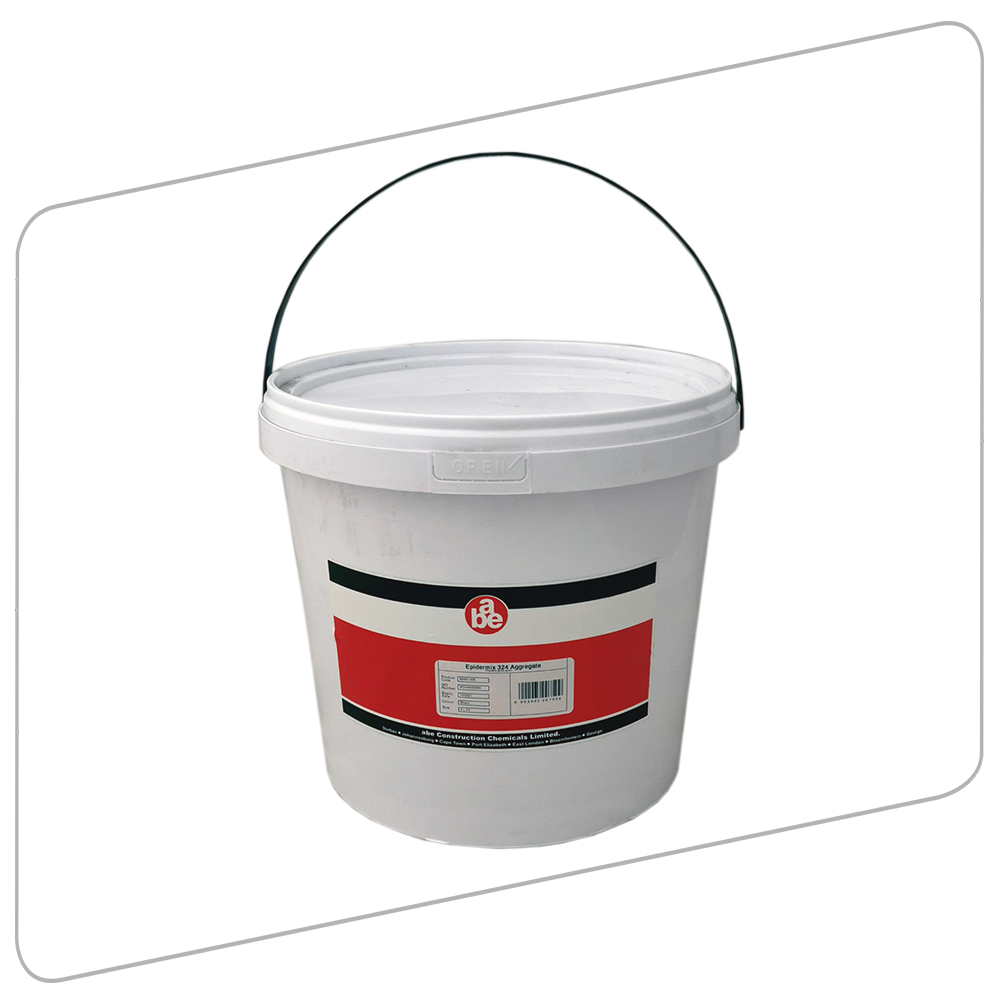
Three-component, solvent-free, aminecured, silica-filled epoxy mortar.
Uses:
Wherever a high strength, flowable, epoxy grout is required.
- Under machine base plates
- Under bridge and other structural bearings
- Grouting holding down bolts, etc
- As a high strength gap filling material
- NOT for use in direct sunlight
Features & Benefits
- Very fluid/flowable
- Super strong grout
- For very narrow access
Surface Preparation
All surfaces against which epidermix 324® will come into contact must be clean, sound and dry. Concrete must be free of laitance, dust, fractured aggregate, oil, grease and foreign matter. For maximum adhesion, surface should be scabbled to expose main aggregate. Steel must be free of oil, grease, old paint, other foreign matter, millscale and rust. For maximum adhesion, surface should be abrasive blast cleaned. Dryness of concrete should be proved by the ‘plastic sheet’ test. There should be no condensate on the underside of a sheet fixed in contact overnight nor should the concrete show a colour change Surface preparation: The substrate must be dry before application Electronic moisture content tests must be conducted prior to application of the priming system. Maximum moisture 4-5% max. (eg Protimeter Survey Master or equivalent) Dynamic Calcium Chloride moisture “weight gain” over 24 hours or (a practical overnight “plastic sheet test” is also advisable approx. 1m² masked down on surface)
Properties of Wet Material
Mixing ratio | Do not split kit |
Density (typical) | 2.05 g/cm3 |
Colour: Base Activator Aggregate Mixed |
Transparent amber Clear Grey-brown Brown |
Flash point | >100ºC |
Dilution | Do not dilute |
Consistency | Binder – low viscosity Mortar – flowable |
Toxicity | Uncured material is toxic |
Properties During Application
Application by | Pouring |
Pot life 5l kit of mortar |
15 ºC – 60 min 20 ºC – 45 min 25 ºC – 30 min 30 ºC – 22 min 35 ºC – 15 min |
Volume solids | 100% |
Curing time @ 25 ºC |
Touch dry – 8 hrs Practical cure – 24 hrs Full cure – 7 days |
Application temperature range | 10 ºC to 40 ºC |
Application rate | At 5 mm thickness, 5 litre kit covers 1m2 – with no wastage allowance |
Equipment cleanup | abe® super brush cleaner |
Properties of Cured Material
Maximum service temperature |
Dry – 90 ºC Wet – 70 ºC |
Compressive strength 7 days at 25 ºC | 110 MPa |
Compressive strength 1 day @ 25 ºC | 60 MPa |
Tensile strength 7 days @ 25 ºC | 9 MPa |
Grouting test – 15 diameter embedment annulus 25% of diameter | 12 mm HT bars fractured |
Modified Arizona shear test using 5mm thick film | High strength prisms failed in concrete |
Shrinkage during cure | Negligible |
Water resistance | Excellent |
Toxicity | Do not use in contact with potable water or food |
Chemical resistance | Resists: oils, greases, petroleum, fuels and solvents, hydrochloric acid, 40% sulphuric acid and caustic soda |
Colour | Brown finish |
Bonding / Priming
Self priming.
Mixing
Premix the silica aggregate to obtain even distribution of the various gradings. Add the entire contents of the activator tin to the base component and, without splashing, stir with a flat paddle until an even, streak free mixture results. This takes at least five minutes. Once liquid components have been thoroughly mixed, the aggregate may be added. When using a mechanical mixer, place mixed liquid in the pan and slowly add premixed aggregate, mixing until an evenly coated, wetted mix results. Use this procedure also if manual mixing is carried out in a drum. All lumps must be broken down and an evenly wetted mass obtained.
Beware high summer temperature and overfast drill mixing causing extremely fast curing. Very low temperature retards/ stops curing.
Coverage
Depends upon dimensions of cavity – to be calculated.
Application
If the unit to be grouted does not form a natural shutter, a tight shutter will have to be provided to retain the epoxy mortar until it has set. Release from the shutter may be obtained through the use of conventional mould oils but a better finish will be obtained by facing the shutter with plastic sheeting. Remove all wrinkles in the plastic to prevent transfer into the epoxy face. Operations must be so designed that there is no chance of air entrapment in the mortar. Pouring must be done from one point, or side, of the unit and must continue from there until the gap is completely filled. Depending on the geometry of the unit and the distance that the grout will have to flow, it is usually necessary to provide a shuttered head for ingress of the mortar. As a simple rule of thumb, the smaller the gap and the longer the distance that the grout will be required to flow, the larger must be the head provided. The volume of epidermix® 324 that can be placed in one lift depends on several factors:
- The ambient conditions prevailing in the immediate vicinity of the repair;
- The heat absorbing properties of the shuttering and the substrate;
- The cross sectional area of the repair;
- The area of surface contact;
- The ease of access for placing the mortar.
Seek the help of a.b.e.®’s Technical Department prior to application to prevent problems arising from the exothermic reaction, where such conditions might apply. As a rough guide, maximum thickness for a single placing under equipment should be 50 mm, taking into account the “heat sink” of the exothermic reaction into the substrate and steel baseplate. Where placing in larger contained volumes, a single placing should not involve more than about 6×5 litre kits of epidermix® 324 (i.e. about 30 litre mortar). Thicker sections require multiple delayed pours to avoid
excessive heat buildup. Shuttering may be stripped as soon as the last lift has set. If appearance is important, rub down any nibs immediately, using a carborundum stone.
Cleaning
abe® super brush cleaner before dried/cured
Protection on Completion
Against traffic and spillage until cured.
Most epoxies chalk and degrade in extensive sunlight.
Temperature & Relative Humidity
See “properties of cured material”, “Properties during application” and “Mixing”.
Model Specification
Three component, high strength, flowable epoxy grout for machine bases and bridge bearing pads. The grout shall be epidermix® 324, a three component, solvent free, amine cured, flowable epoxy comprising a resin hardener system and pre-packed aggregates applied in accordance with the manufacturers recommendations, The mortar shall have a compressive strength of 110 MPa in seven days and be resistant to aliphatic solvents, oils, petrol, diesel fuel, and chemical attack.
Packaging
epidermix® 324 is supplied in 5L kits.
Handling & Storage
This product has a shelf life of 24 months if kept in a dry cool place in the original packaging. In more extreme conditions this period might be shortened.
Health & Safety
Uncured epidermix® 324 contains diethylene triamine which is toxic. Prolonged skin contact can result in dermatological reaction. Always ventilate a working area very well during application and curing. Always wear gloves and eye protection when working with the material and avoid excessive inhalation and skin contact. If material is splashed into the eye, wash with copious quantities of clean water and seek medical advice.
Cured epidermix® 324 is inert but must not be allowed to come into contact with foodstuff or potable water. When transporting liquids and semi-liquids by aircraft, ask for material safety data sheet.
Important Note
This data sheet is issued as a guide to the use of the product(s) concerned. Whilst a.b.e.® endeavours to ensure that any advice, recommendation, specification or information is accurate and correct, the company cannot accept any liability for application – because a.b.e.® has no direct or continuous control over where and how a.b.e.® products are applied.
Further Information
Where other products are to be used in conjunction with this material, the relevant technical data sheets should be consulted to determine total
requirements.
a.b.e.® has a wealth of technical and practical experience built up over the years in the company’s pursuit of excellence in building and construction
technology.