Two-component, epoxy adhesive/repair compound
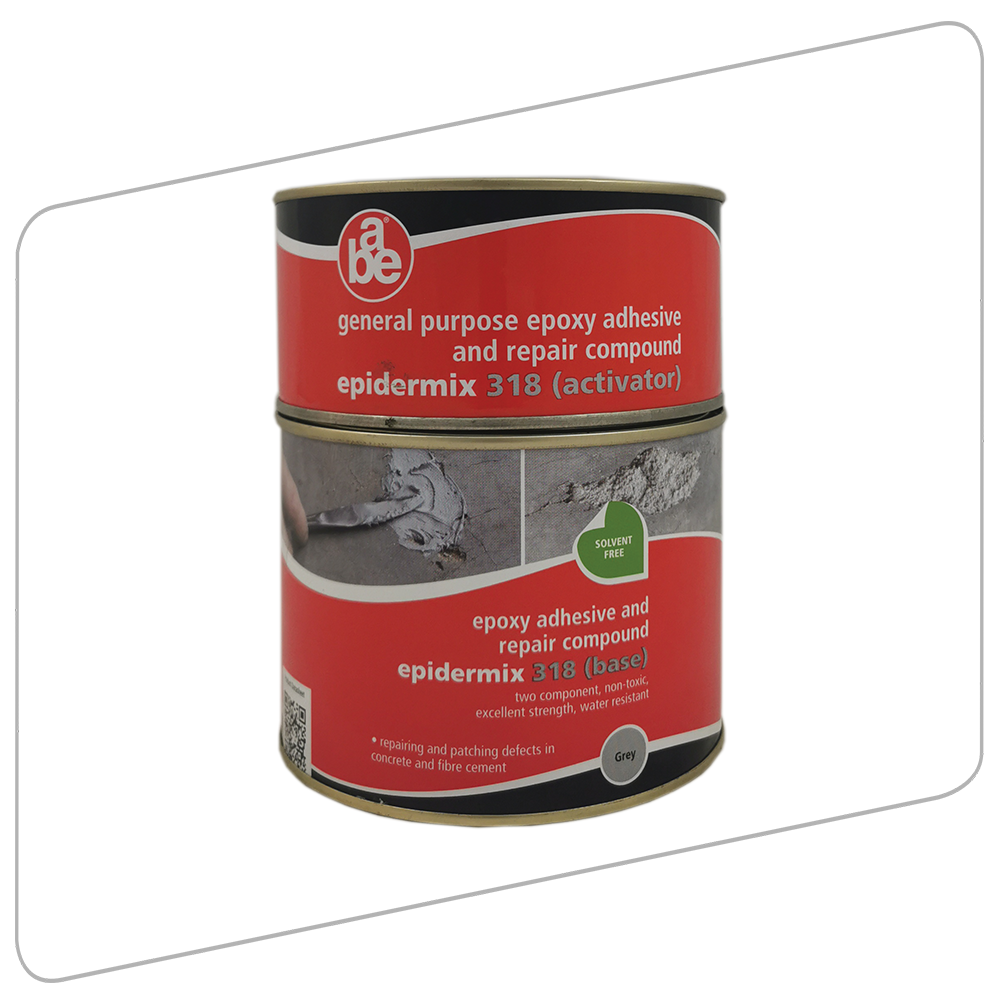
Two component, solvent free, filled, polyamide cured epoxy.
Uses:
Repairing and patching defects in concrete, fabricating components and repairing defects in fibre cement products. epidermix® 318 is damp tolerent.
The viscosity of epidermix® 318 is sufficient to hold its place on horizontal and vertical faces.
Surface Preparation
Any surface to be repaired with epidermix® 318 must be clean, mechanically sound, dry or damp. The surface should be chipped to expose main aggregate and in the case of honeycomb, all suspect material must be cut out. The surface must be free of all debris prior to placing the compound.
Mixing
Set up equal volumes of Base and Activator side by side on a clean board. Do not take more than about 250 ml of each compound. Mix thoroughly with a trowel or spatula.
Application
Mixed epidermix® 318 should be pressed into place in the repair area using a small amount first to wet out the surface and then building up the required thickness. The viscosity of epidermix® 318 is sufficient to hold its place in soffit repairs and on vertical faces. If the volume is too big to repair in one placing, leave the contact surface rough to act as a key for a subsequent placing once the first one has set.
A final smooth finish may be obtained by trowelling off the surface of the still uncured epidermix® 318 with a water dampened steel trowel.
Properties of Wet Material
Mixing ratio | 1 base : 1 activator by volume or mass |
Density (typical) | 1,7 g/cm3 |
Colour:Base Activator Mixed material |
Off white Grey Grey – approximate to concrete |
Finish | Trowelled to smooth finish with water wet steel trowel |
Flash point | Nil |
Dilution | Not to be diluted |
Consistency | Each component is a heavy paste |
Toxicity | Uncured material is toxic |
Shelf life | 2 years from date of manufacture |
Storage conditions | Store under cover in cool conditions |
Properties of Application
Application by | Gloved hand and/or steel trowel |
Pot life | 60 to 100 mins/500ml @ 25º C |
Volume solids | 100% |
Theoretical coverage | 1m2/l on smooth surface |
Maximum recommended thickness per layer | 15 mm |
Curing time @ 25º C | Touch dry : 2 hours Practical cure : 12 hours Full cure : 7 days |
Overcoating time @ 25º C | Min : 4 hours Max : 23 hours |
Application temp. range |
10º C to 40 º C |
Fire resistance of wet material | Non-flammable |
Equipment clean up | a.b.e.® super brush cleaner |
Properties of Cured Material
Max service temperature | Dry : 70º C Immersion : 60º C |
Compressive strength @ 25º C | 60 MPa in 24 hrs 75 MPa in 7 days |
Tensile strength @ 25º C | 17 MPa |
Lap shear on grit blasted steel | 8 MPa using 2mm bond line thickness |
Shrinkage during curing | Negligible |
Chemical Properties of Cured Film
Toxicity | Non-toxic after curing |
Water resistance | Excellent |
Solvent resistance | Resists aliphatic solvents, oils, petrol, diesel fuel. |
Chemical resistance | Resists dilute inorganic acids and dilute alkalis |
Health & Safety
Uncured epidermix® 318 must be regarded as toxic. Gloves should be worn at all times and care must be taken not to ingest any of the material by eating or smoking while working with the compound. If working in a confined space, provide adequate ventilation.
Clean tools with abe® super brush cleaner and use a little of this liquid to remove any splashes on the skin. Wash finally with soap and warm water.
Cured epidermix® 318 is inert and non-toxic.
Packaging
epidermix® 318 is supplied in 200ml, 500ml, 1 litre and 4 litre kits.
Handling & Storage
Epoxy compounds in their uncured state are toxic and prolonged skin contact can give rise to dermatitis. When handling epoxy compounds, use should always be make of disposable gloves and barrier creams. Involuntary habits such as face starching and spectacle adjustment must be avoided. Similarly eating and smoking whilst or after working with epoxy must be avoided until the individual has washed up. This product has a shelf life of 24 months if kept in a cool dry place.
Important Note
This data sheet is issued as a guide to the use of the product(s) concerned. Whilst a.b.e.® endeavours to ensure that any advice, recommendation, specification or information is accurate and correct, the company cannot accept any liability for application – because a.b.e.® has no direct or continuous control over where and how a.b.e.® products are applied.
Further Information
Where other products are to be used in conjunction with this material, the relevant technical data sheets should be consulted to determine total
requirements.
a.b.e.® has a wealth of technical and practical experience built up over the years in the company’s pursuit of excellence in building and construction
technology.
Please consult our website for our latest datasheets.