Mortar and screed improver and adhesive
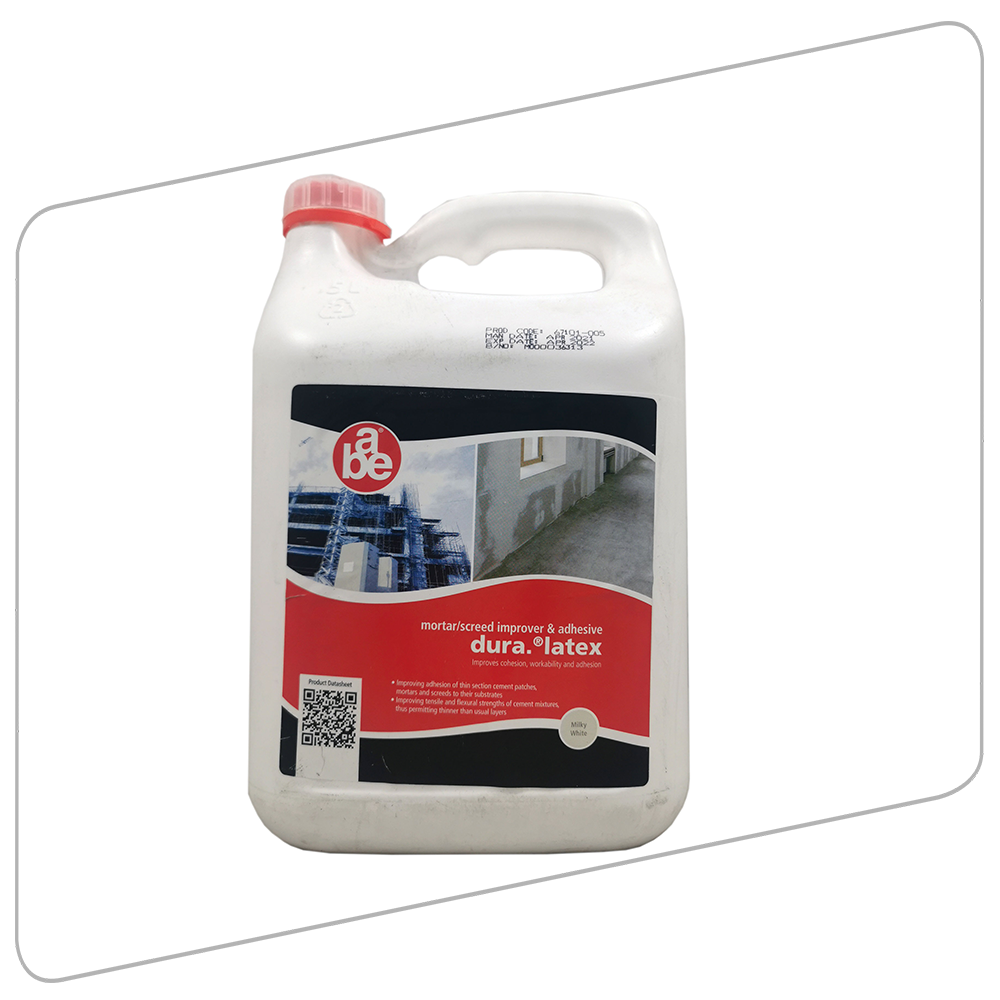
duralatex is a synthetic resin polymer which is supplied as a ready to use liquid. It is designed to improve the qualities of site-batched cementitious mortars and slurries. Being resistant to hydrolysis, it is ideal for internal and external applications in conjunction with cement.
Uses:
- Improving adhesion of thin section cement patches, mortars and screeds to their substrates.
- Improving tensile and fl exural strengths of sand/cement mixtures thus permitting thinner than usual layers.
NOTE: duralatex is NOT a concrete structural adhesive. In such cases use epidermix® 344.
Advantages
- Single-component liquid can be easily gauged as required
- Improves cohesion and workability
- Improves mortars to provide waterproof repairs, renders and toppings that are highly resistant to freeze/thaw cycling
- Improves tensile and flexural properties allowing thin applications
- Excellent bond to concrete, masonry, stonework, plaster and blackboard
- Contains no chlorides
- Can be applied to damp substrates
Surface Preparation
Any surface to be screeded, plastered or patched must be thoroughly clean and sound. It must be free from grease, oil and any other foreign matter. Laitance, dust, loose particles and any spalling or flaking surface must be removed.
Porous surfaces such as concrete brickwork must be thoroughly dampened to kill suction. Soaking should continue for some 12 hours prior to an application being made. At the time of the application no free water or ponding must be present on the surface.
Typical Physical Properties of Wet Material
Consistency | Liquid |
Density | 1,00 g/cm3 |
Colour |
Wet: milky white Dry:Translucent clear |
pH value | 11 |
Dilution | Clean water |
Properties During Use
Consumption
As an Adhesive Slurry:
±500 ml duralatex/m2 (figures are approximate as the quantity of duralatex used to produce workability will depend on variations in mix’s water demand).
In a Mortar:
±1,50 ℓ duralatex/m2 @ 12 mm thickness.
±1,75 ℓ duralatex/m2 @ 15 mm thickness.
±2,00 ℓ duralatex/m2 @ 20 mm thickness.
±2,25 ℓ duralatex/m2 @ 25 mm thickness.
±2,50 ℓ duralatex/m2 @ 30 mm thickness.
Properties of Final Material
These vary widely being affected by the quality of the aggregate, the aggregate/cement ratio used and the cement/ liquid ratio achieved under the particular water demand of the aggregate. The thoroughness of post curing of the mortar will also play a significant role.
TENSILE STRENGTH: improved by ±40%
FLEXURAL STRENGTH: improved by ±45% using 3:1 sand-cement mortar as a control.
CHEMICAL RESISTANCE: This is not improved over the performance of normal cementitious materials.
SOLVENT RESISTANCE: duralatex is attacked by solvents.
Bonding / Priming (Adhesive Slurry for Priming)
The gauging liquid consists of equal volumes of duralatex and clean potable water. Adhesive slurry is made from equal parts of clean dry sand (up to 3 mm particle size) and ordinary Portland cement. These are dry mixed and then gauged with sufficient gauging liquid to give a viscous but easily brushed consistency. The slurry is brushed well into the pre-dampened substrate using a stiff broom or brush.
Mixing
Stir well before use.
Coverage
Dependant on application and thickness of application.
Application
Production and Placing of Mortar
The gauging liquid composition will vary depending upon the thickness of the mortar layer to be placed. Mortars up to 12 mm thickness are gauged with 1 volume duralatex to 1 volume water.
Mortars between 12 – 20 mm thickness are gauged with 1 volume duralatex to 2 volumes water. Mortars exceeding 20 mm thickness are gauged with 1 volume duralatex to 3 volumes water. Mortars are ideally mixed in a pan mixer and mixing time should not exceed 2 minutes to keep air entrapment to a minimum.
A mortar is made from 2 to 4 volumes of dry aggregate – not exceeding maximum 3 mm particle for plasters or 8 mm particle for screeds – dry mixed with 1 volume ordinary Portland cement.
This mix is then gauged with the appropriate gauging liquid to produce a stiff but workable material – a so-called earth damp consistency. The mortar is applied to the still wet slurry, consolidated, levelled and smoothed following good plastering or screeding practice. Finishing is made easier if tools are wetted from time to time with duralatex.
Cleaning
Tools, brushes and mixing equipment should be cleaned immediately after use and before material has set with a.b.e.® super brush cleaner followed by washing with soap and water.
Protection on Completion
The newly applied mortar must be protected from rain, direct strong sunlight and wind since too rapid drying will produce shrinkage, cracking and reduce cohesion. The newly laid surface must be kept damp for at least 5 days to promote good curing of the Portland cement.
Temperature & Relative Humidity
Do not apply concrete / screeds if temperature is below 5° C
Model Specification
The adhesive screed improver will be duralatex, a single-component, latex polymer, applied in accordance with the recommendations of a.b.e.® .
Packaging
1 ℓ, 5 ℓ, 25 ℓ and 200 ℓ containers.
Handling & Storage
Product safety information required for safe use is not included. Before handling, read product and safety data sheets and container labels for safe use, physical and health hazard information. The safety data sheet is available from your local a.b.e.® sales representative.
Health & Safety
Product safety information required for safe use is not included. Before handling, read product and safety data sheets and container labels for safe use, physical and health hazard information. The safety data sheet is available from your local a.b.e.® sales representative.
Important Note
This data sheet is issued as a guide to the use of the product(s) concerned. Whilst a.b.e.® endeavours to ensure that any advice, recommendation, specification or information is accurate and correct, the company cannot accept any liability for application – because a.b.e.® has no direct or continuous control over where and how a.b.e.® products are applied.
Further Information
Where other products are to be used in conjunction with this material, the relevant technical data sheets should be consulted to determine total
requirements.
a.b.e.® has a wealth of technical and practical experience built up over the years in the company’s pursuit of excellence in building and construction
technology.