Cementitious flexible waterproofing slurry
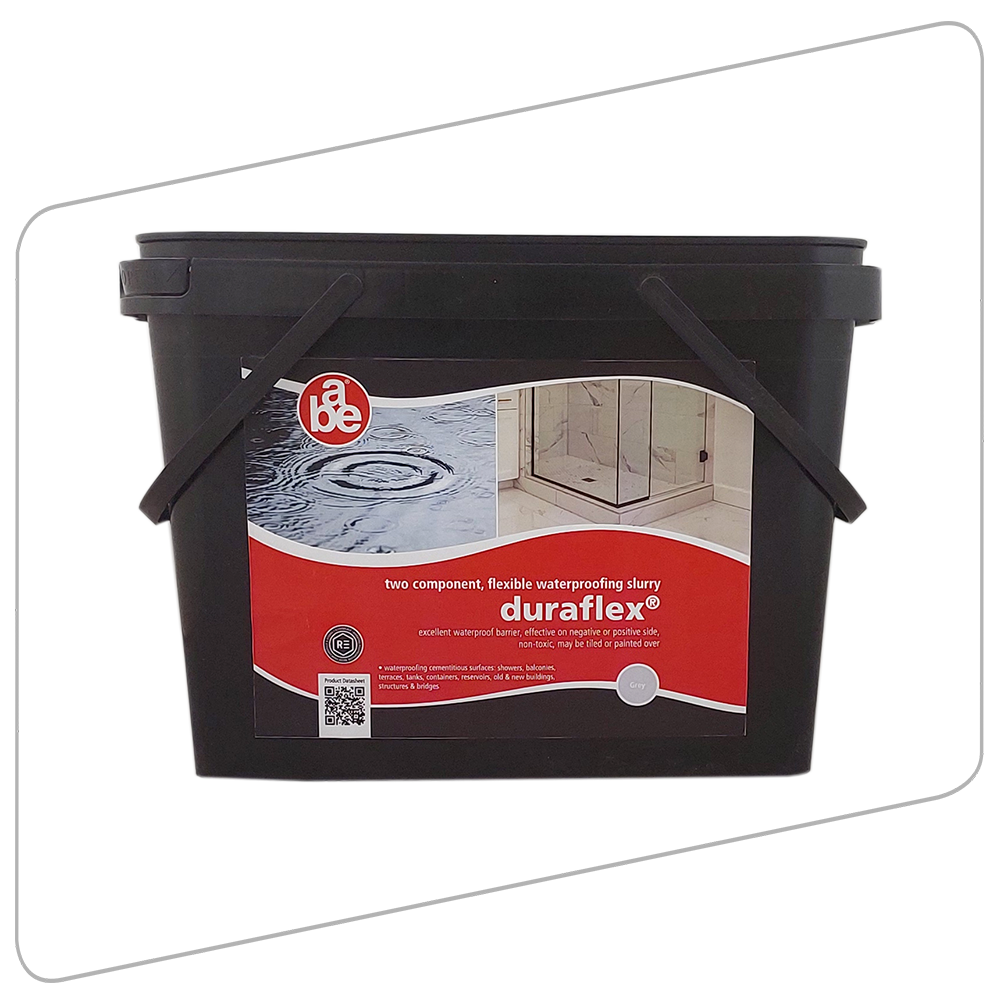
duraflex® is a ready to use flexible slurry based on a special synthetic resin dispersion and a blend of selected cement mixed with carefully graded aggregate.
Uses:
duraflex® is used for:
- Protection and repair of balconies, terraces and haunching concrete of roads and bridges.
- Waterproofing of new and old buildings (internal and external).
- Waterproofing of tanks, containers and water reservoirs.
Advantages
- Excellent waterproof barrier.
- Effective on negative or positive side.
- High bond strength.
- Excellent freeze/thaw resistance.
- Excellent resistance to chloride ion penetration.
- Brush, trowel, or spray applied.
- Reliable application.
- Self-curing.
- Low in place cost.
- Non-toxic.
- Good abrasion resistance.
- Approved for use in potable water systems.
Bonding / Priming
No priming required.
Surface Preparation
All surfaces that are to receive the coating must be free from oil, grease, wax, dirt or any other form of foreign matter that might affect adhesion. Typically concrete may require grit blasting. Spalled surfaces or those containing large blowholes and other such defects should be repaired using duraflex® or an a.b.e.® approved repair mortar. Care must be taken when choosing the repair mortar to ensure that it has all necessary approvals for contact with potable water. If the surface contains small blow holes, typically less than 1 mm wide, the coating can be applied directly onto the substrate without the need for a treatment. Cracks which are less than 0.3 mm in width can be over-coated as long as the crack is not likely to open up to greater than 0.3 mm (this is greater than the maximum permissible crack widths recommended in BS 8007:1987, the British Standard Code of Practice for the design of concrete structures for retaining aqueous liquids). Cracks that are greater than 0.3 mm in width should be chased-out to 4 mm in width and approximately 15 mm in depth. This should be filled with duraflex® (applied using less liquid providing a thicker consistency). When the material in the crack has hardened the coating should be applied over the crack.
Typical Physical Properties
Nominal coverage | 2 kg/m2/mm thick/coat (2 coats required) |
Pot life | @ 10 ºC – 2 hours @ 20 ºC – 1 hour @ 30 ºC – 0.5 hours |
Hardening time | Resistant to mechanical stress: 3 days Full cure: 7 days |
Resistance to water pressure | Attained after 7 days cure Positive pressure: 10 bar Negative pressure: 4 bar |
Equivalent concrete cover | 180 mm |
Mixing
It is essential to use a mechanical mixer, such as a slow speed electric drill fitted with a suitable paddle. Our Technical Department will be pleased to supply details of blade design.
Fill approximately three quarters of component A (milky liquid) into a pail and, with continuous stirring, slowly add component B (greyish powder). Mixing must be continued until the mix is homogeneous and free of lumps.
For horizontal surfaces such as the base of reservoirs, add the remaining component A. For other applications add only sufficient component A to provide a suitable consistency. When the two components are mixed together, a plastic thixotropic liquid results which is easy to apply.
The very finely dispersed resin component imparts excellent adhesion to concrete, plaster, and natural stone surfaces.
Once cured, duraflex® is waterproof and resistant to weathering. It exhibits a high degree of impermeability to water vapour and carbon dioxide. The cured coating is highly flexible and may be used to overbridge hairline cracks up to 0.2 mm in width. duraflex® is nontoxic and contains no chlorides.
Coverage
Nominal coverage rate: 8 m2/15 kg for 1 mm wet film thickness. The coverage figure given is theoretical due to wastage factors and the variety and nature of possible substrates, practical coverage figures will be reduced. A minimum coverage of 2 kg/m2/mm applied in not less than two coats which is recommended.
Pre-dampening The Substrate
Thoroughly dampen the substrate surface with clean water using a brush, roller or spray. Substrates having a high porosity will require more dampening. Do not apply the coating when the substrate is wet, but allow the water to soak in until the substrate is just visibly damp before proceeding. Any excess water must be removed using a sponge. The surface should be SSD (surface saturated dry).
Application
duraflex® may be applied to the correctly prepared surface by short bristled block brush, rubber squeegee, trowel or spray.
Brush: using a block brush, duraflex® should be applied in three coats to provide a final dry film thickness of between 2 – 3 mm on surfaces. Alternate coats should be applied at right angles to each other, allowing 16 hours between coats.
Trowel: horizontal surfaces – the first layer of duraflex® should be applied to a thickness of 1 – 1.5 mm. Allow to cure for approximately 16 hours and then apply a second layer using a steel float. duraflex® should not be applied thicker than 1.5 mm per coat.
The first coat must be allowed to cure, hard to the touch, before the second coat is applied. There is no maximum over coating time but the surface must be kept clean.
The temperature and humidity will have an effect on the rate of curing, at lower temperatures and humidity curing may take up to 16 hours.
Pre-dampening of the surface of subsequent coats is not necessary.
Spray: contact our Technical Department for details of the special equipment required.
The appropriate PPE must be used when mixing and applying the duraflex® See the MSDS for further information.
Reinforcement with a.b.e.®mesh
abe® mesh may be incorporated to reinforce the duraflex® at joints and cracks. abe® mesh should be bedded into the first coat while still wet.
Immediately after placing apply a further thin coat of duraflex® to ‘wet’ out the abe® mesh.
Allow the first coat to set before applying the second coat.
Cleaning
Tools, brushes and mixing equipment should be cleaned immediately after use and before material has set with a.b.e.® super brush cleaner followed by washing with soap and water.
Protection on Completion
duraflex® may be left as is, or:
- Be tiled over.
- Painted with high quality PVA acrylic paint.
Temperature & Relative Humidity
Application temperature: 5°C to 40°C.
Do not apply if rain is imminent.
Model Specification
Two-component, flexible waterproofing slurry. The waterproofing compound shall be duraflex®, a two component, polymer modified, cementitious coating applied in accordance with the manufacturers recommendations, a.b.e.®. The coating shall conform to the requirements of EMPA test 235’528, EMPA test 162’475/2 and UK Water Byelaws Scheme (WRc Listed). The compound shall have a resistance to positive pressure of 10 bar and a resistance to negative pressure of 4 bar.
Packaging
duraflex® is supplied in 15kg kits.
Handling & Storage
This product has a shelf life of 12 months if kept in a dry cool place in the original packaging. In more extreme conditions this period might be shortened.
Health & Safety
duraflex® powder is irritating to eyes, respiratory system and skin. Avoid inhalation of dust and wear suitable respiratory protective equipment. duraflex® liquid is not classified as dangerous. duraflex® when mixed becomes highly alkaline.
Wear suitable protective clothing, gloves and eye protection. For both components and mixed material avoid contact with skin and eyes. In case of contact with eyes or skin rinse immediately with plenty of water and seek medical advice.
Important Note
This data sheet is issued as a guide to the use of the product(s) concerned. Whilst a.b.e.® endeavours to ensure that any advice, recommendation, specification or information is accurate and correct, the company cannot accept any liability for application – because a.b.e.® has no direct or continuous control over where and how a.b.e.® products are applied.
Further Information
Where other products are to be used in conjunction with this material,the relevant technical data sheets should be consulted to determine total requirements.
a.b.e.® has a wealth of technical and practical experience built up over the years in the company’s pursuit of excellence in building and construction technology.
Please consult our website for our latest datasheets.