Liquid epoxy grouting compound
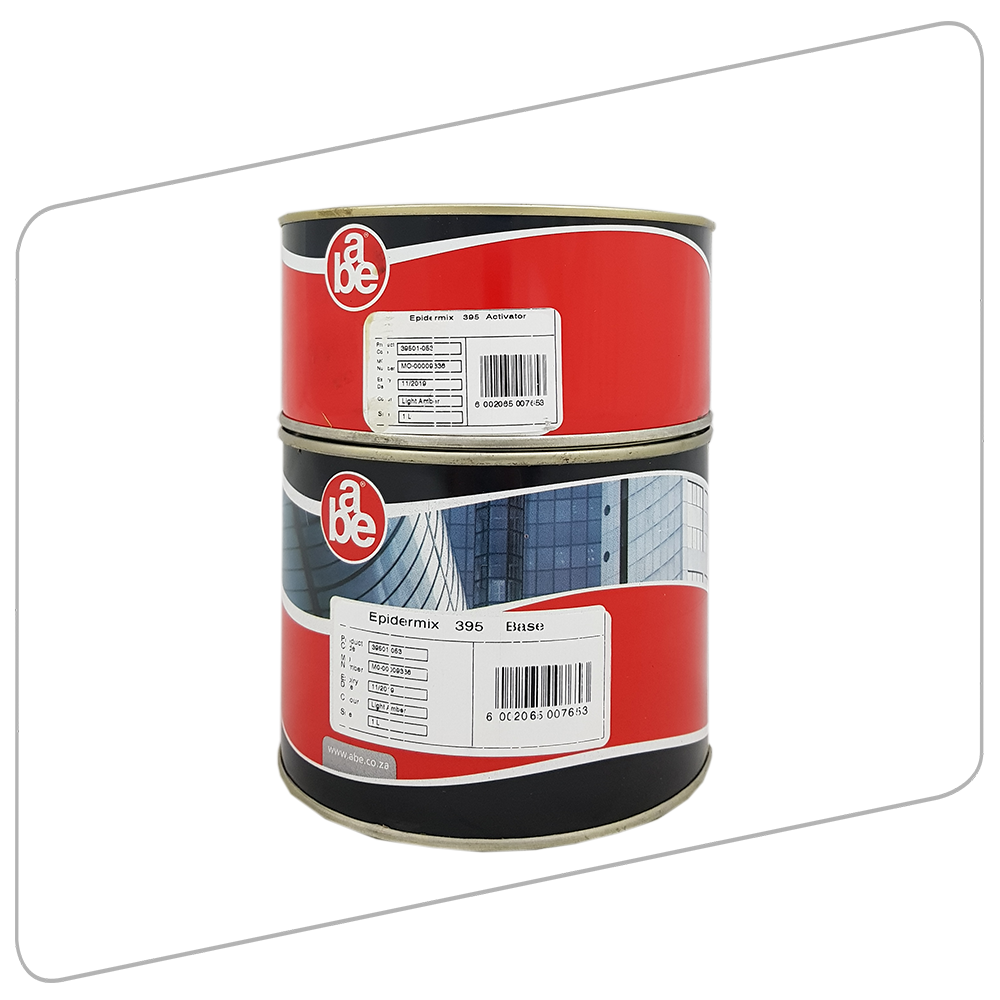
Two-component, modified-epoxy liquid.
Uses:
As a grouting medium, either as supplied or converted into a mortar, for fixing starter bars, bolts and other similar items, vertically down into concrete or rock. As a flowable grout or bedding for areas of awkward access. As a fast-setting crack repairing compound.
Uses
As a grouting medium, either as supplied or converted into a mortar, for fixing starter bars, bolts and other similar items, vertically down into concrete or rock. As a flowable grout or bedding for areas of awkward access. As a fast-setting crack repairing compound.
Advantages
- Stronger than surrounding concrete and steel
- Easy pouring for upstanding bolts and concrete road/slab cracks
- Easy access to narrow gap horizontal areas
Design Criteria
Given adequate concrete strength and provided that a bar of deformed or threaded steel, either mild or high tensile, is embedded to a depth of at least 15 diameters, it can be expected that any failure of the assembly will be due to tensile rupture of the steel. Thus epidermix® 395 grouting allows the steel and the concrete to operate at full design strength. Regarding the diameter ratio of hole to rod, it has been shown that the ultimate average bond strength is at its maximum at a ratio of 1,3:1. Ultimate average bond stress reduces as the hole:rod ratio increases to a value of 1,67:1. Thereafter it remains constant. An increase of diameter ratio from 1,3 to 1,67 will reduce the ultimate average bond strength by some 20%.
Surface Preparation
All surfaces must be clean, sound and dry. Cast concrete must be free of all laitance, dust and foreign matter.
Drilled concrete and rock must be free of dust and debris and if wet-drilled must be dry and free of all traces of slurry. Any glaze caused by core drilling must be removed by mechanical roughening to ensure good bonding between the adhesive and the concrete / rock surface. Close-fitting burrs attached to a long shaft mounted in a power drill will aid in this respect. Pockets must be both free of standing water and surface dry. Smooth steel should be abrasive blast cleaned, and must be free of scale, rust and oily material. Deformed and threaded bars should be oil and grease free and must be free of rust and scale.
Properties of Wet Material
Mixing ratio | Do not split kit |
Density | 1.09 g/cm3 |
Colour: Base Activator Mixed |
Transparent, light amber Transparent, dark amber Clear amber |
Flash point | > 100 ºC |
Dilution | Do not dilute |
Consistency | Low viscosity liquid |
Toxicity | Uncured material is toxic |
Shelf life | 2 years from date of manufacture |
Storage conditions | Store under cover in cool place |
Packaging | 500 ml, 1 L, 2 L kits |
Properties During Application
Application by | Pouring or injection gun. As a flowable mortar by pouring |
Work life (as mortar- 500ml kit) |
15 °C – 80 min. 20 °C – 60 min. 25 °C – 40 min. 30 °C – 30 min. 35 °C – 20 min. |
Work life (as mortar – 1l kit) |
15 °C – 60 min. 20 °C – 45 min. 25 °C – 30 min. 30 °C – 22 min. 35 °C – 15 min. |
Volume solids | 100% |
Curing time @ 25 ºC | Touch dry : 6 hrs Practical cure : 12 hrs Full cure : 7 days |
Application temperature range | 10 °C – 40 °C Temperature of metal to be grouted should not exceed 25 °C at time of grouting. If application temperatures are above 30°C consult a.b.e.® Technical Department for special precautions. |
1l mixed, unfilled epidermix® 395 will be sufficient for : 1l annulus volume | |
Application rate | 1l mixed epidermix® 395 filled with dry silica grit will be sufficient for approx. 1,9l annulus vol. filled at a loading of 1,5 :1 Approx 2l annulus vol. when filled at loading of 2 :1. None of these figures allow for any wastage, which can run as high as 20% – 25%. |
Maximum application rate | Do not grout unfilled epidermix® 395 into a hole larger than 1,5 times bar diameter. When grouting with filled epidermix® 395, annulus width should be kept as small as possible. |
Fire resistance of wet material | Non-flammable |
Equipment clean- up | abe® super brush cleaner. |
Properties of Cured Material
Maximum service temperature | 70 ºC |
Water resistance | Not recommended for structures permanently immersed in water. |
Solvent resistance | Resists aliphatic solvents, vegetable and mineral oils and greases, petroleum fuels |
Compressive strength @ 25 °C: | |
Unfilled | 75 MPa @ 7 days |
+1,5 vol silica filler | 90 MPa @ 7 days |
Tensile strength @ 25 ºC: | |
Unfilled | 34.1 MPa @ 7 days |
Modified Arizona Shear Test | 55 MPa (Prisms failed in concrete) @ 7 days |
Grouting test 15 diameter embedment, annulus 25% of diameter | 12mm HT bars fractured |
Shrinkage during curing | Negligible |
Colour | Transparent amber |
Overlap Shear Strength
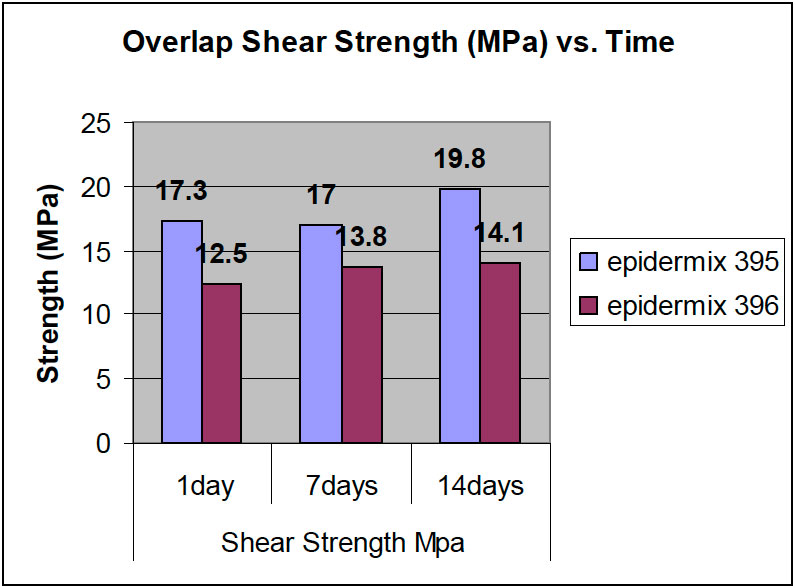
Bonding / Priming
Self priming.
Consumption Calculation
The quantity of epidermix® 395 required may be calculated from the formula:
0,8 (D+d)(D-d) HN = Litres of grout required
1 000
where:
D = diameter of hole in cm
d = diameter of metal in cm
H = depth of hole in cm
N = number of holes
This gives a figure for liquid consumption without any allowance for wastage. A filled grout will require about 0,6 of this quantity of liquid when filled 1,5:1.
Mixing
Stir both containers individually and ideally use a can opener to remove the lip of the containers. Add the entire contents of the activator tin to the base and stir with a flat paddle until an even streak-free mixture results. This takes at least five minutes. If a mortar is required, premix the base and activator and then add silica grit aggregate. Up to two volumes may be used and the whole mixture must be stirred until the aggregate is evenly wetted.
Overlap Shear Strenght
Download datasheet to view table.
Application
For best results mixed material should be poured into the hole to such a level that when the bar is inserted, material displaced just reaches the top of the hole. Bar should be inserted into the compound with a rotary motion to ensure full wetting of both bar and concrete faces. Do NOT merely drop the bar in as this can result in air entrapment. If the bar is already positioned, pour compound slowly into the annulus, punning with a piece of suitable wire to help release air bubbles. If it is important that the bar must remain vertical, a jig or template must be used until the compound has set. Where epidermix® 395 mortar is being used to bed an object (i.e. fill a gap between horizontal surfaces) pouring must be done from one point only, to prevent air entrapment.
Provision must be made for any entrapped air to escape by venting, if necessary. If shuttering has to be provided to retain the grout whilst setting, shutters must be treated with a release agent or faced with plastic sheeting.
It will be necessary to provide an inlet point into the shuttering so that a head of compound can be built up to promote flow. Again venting must be provided.
Cleaning
abe® super brush cleaner before dried/cure.
Protection on Completion
Against traffic and spillage until cured.
Temperature & Relative Humidity
See “Properties of Cured Material” and “Properties During Application”.
Model Specification
Two component structural liquid epoxy grouting compound for fixing starter bars vertical down, holding down bolts etc. Low creep. The grouting compound shall be epidermix® 395, a two component, flowable structural liquid epoxy applied in accordance with the manufacturers recommendations, a.b.e.®
Packaging
epidermix® 395 is supplied in 500ml, 1l and 5l metal containers.
Handling & Storage
This product has a shelf life of 24 months if kept in a dry cool place in the original packaging. In more extreme conditions this period might be shortened.
Health & Safety
Product safety information required for safe use is not included. Before handling, read product and safety data sheets and container labels for safe use, physical and health hazard information. The safety data sheet is available from your local a.b.e.® sales representative.
Important Note
This data sheet is issued as a guide to the use of the product(s) concerned. Whilst a.b.e.® endeavours to ensure that any advice, recommendation, specification or information is accurate and correct, the company cannot accept any liability for application – because a.b.e.® has no direct or continuous control over where and how a.b.e.® products are applied.
Further Information
Where other products are to be used in conjunction with this material, the relevant technical data sheets should be consulted to determine total
requirements.
a.b.e.® has a wealth of technical and practical experience built up over the years in the company’s pursuit of excellence in building and construction
technology.