Professional liquid waterproofing compound
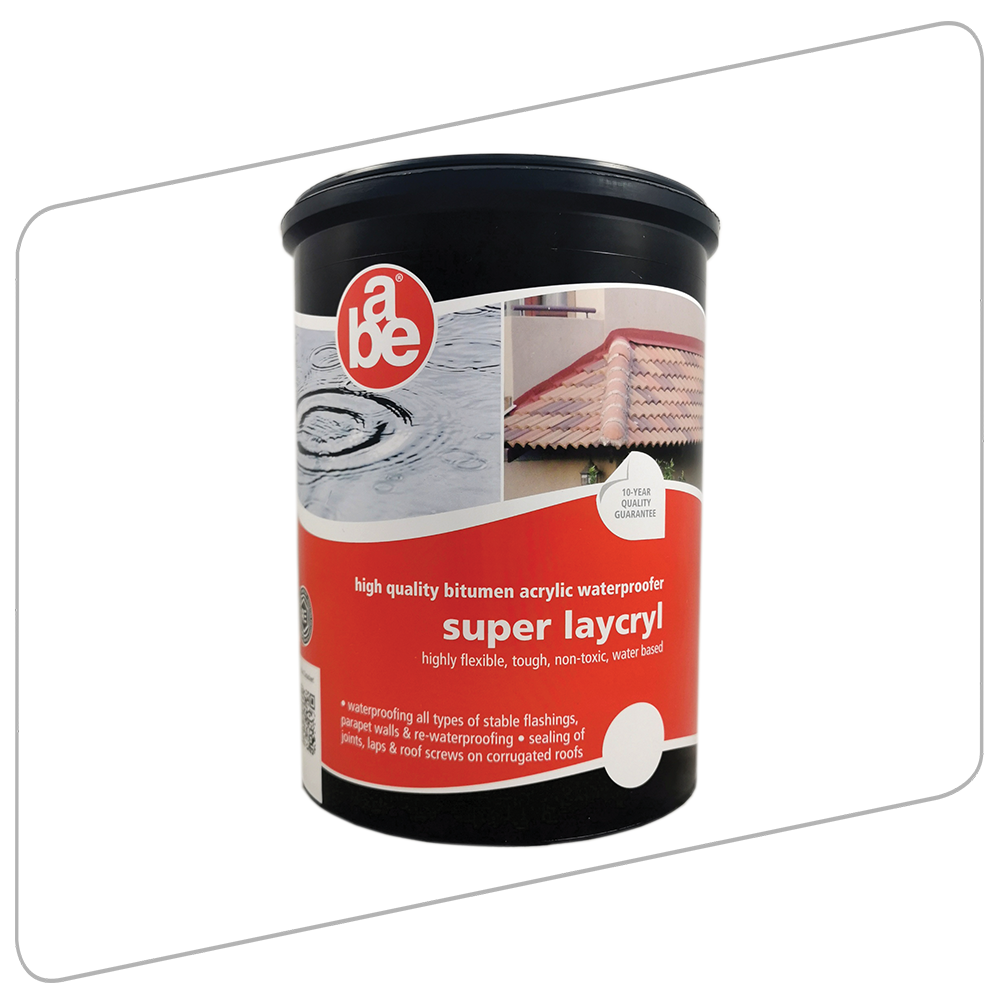
super laycryl® is a highly flexible liquid applied emulsion reinforced with abe®membrane to provide an in situ, seamless professional waterproofing system.
super laycryl® is recommended for:
- All types of flashings
- Parapet walls
- Flat roof waterproofing
- Re-waterproofing over existing waterproofing systems
- Sealing of joints, laps and roofing screws on corrugated roofs
- The system is for non-trafficable roofs
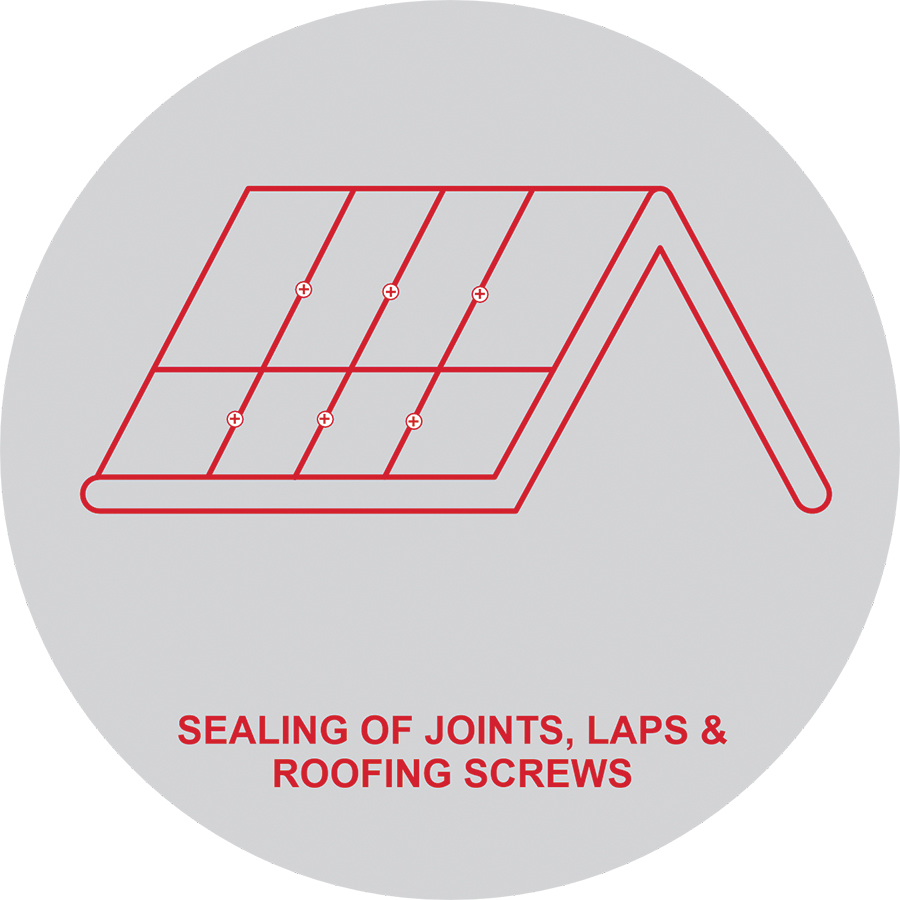
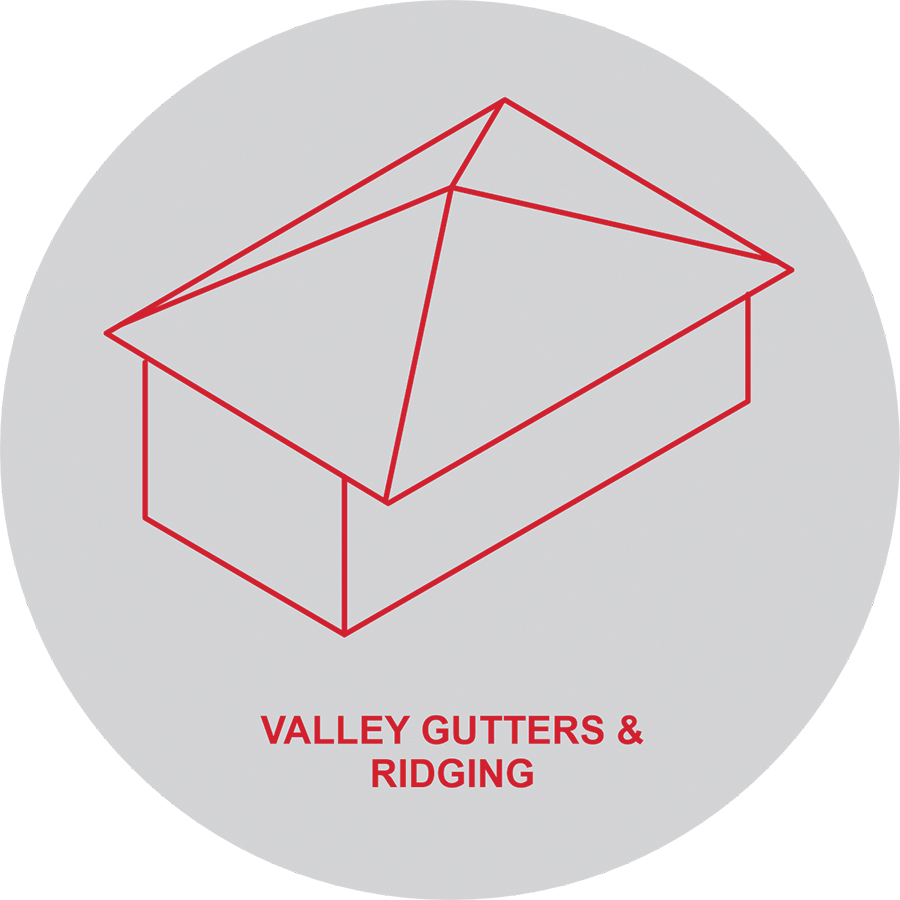
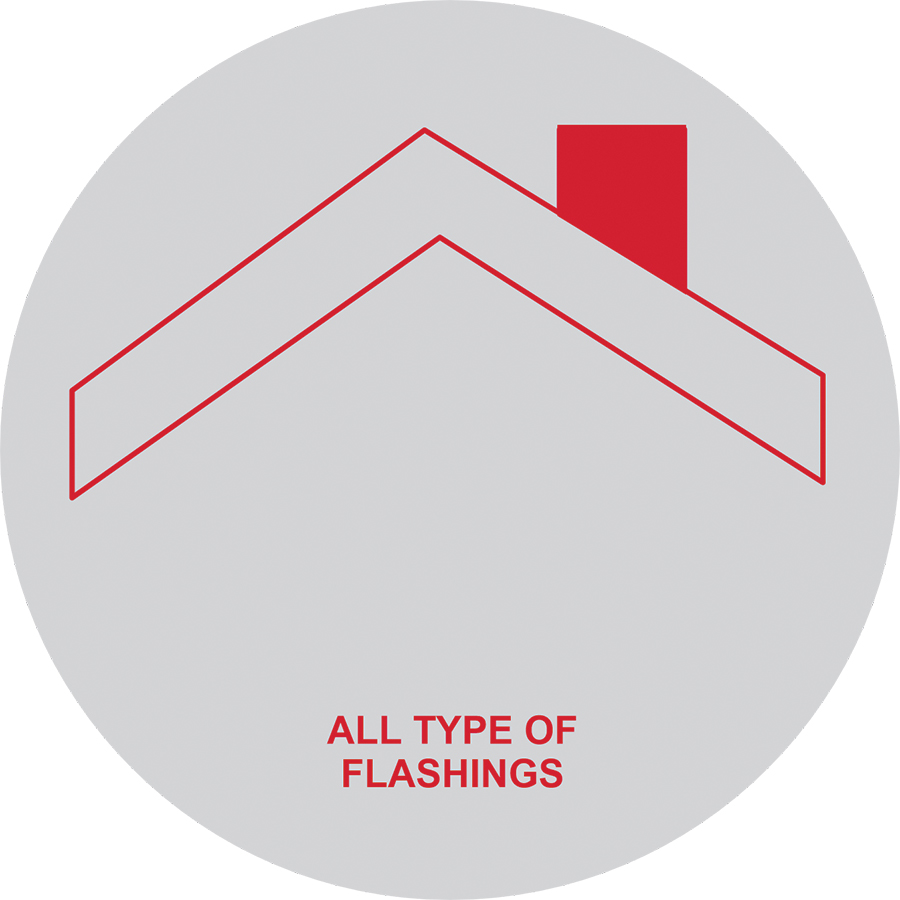
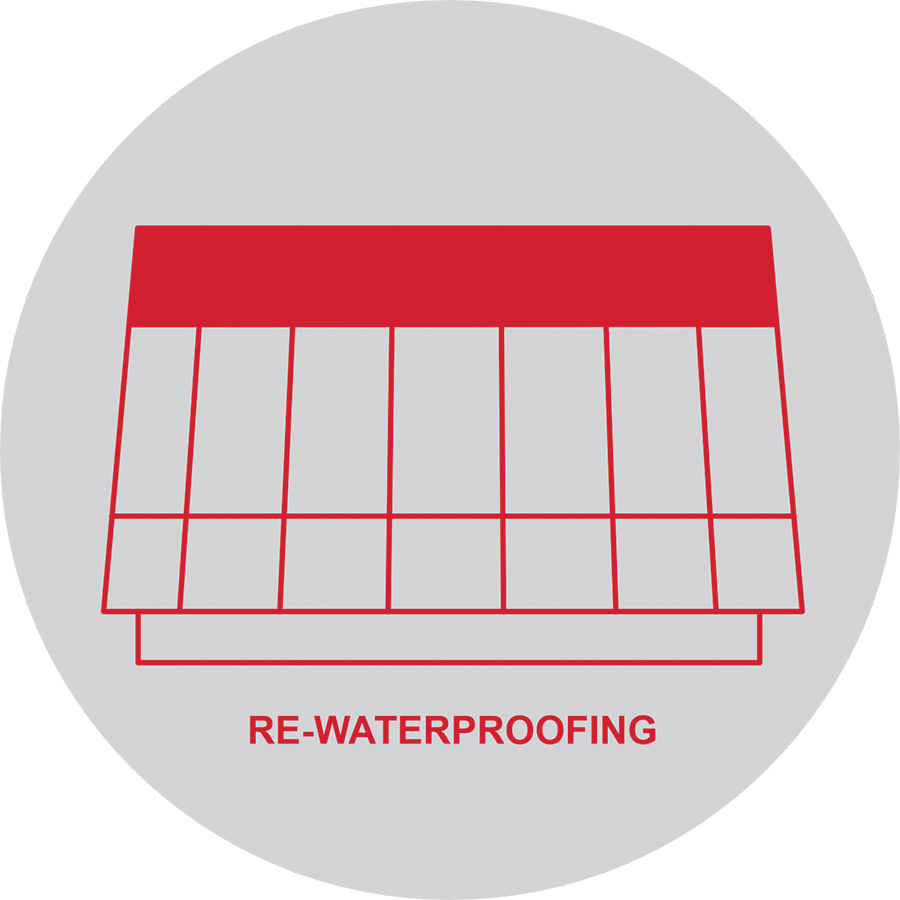
Advantages
- super laycryl® is an all-in-one system
- There is no need for separate primers (apart from metal surfaces) or top coats
- It has excellent weathering properties, adhesion and is tough, flexible and non-toxic
- It comes in a wide range of colours
- 10-year conditional product warrantee
Surface Preparation
All surfaces to be clean, dry, sound and free of all laitance, grease, oil or loose and flaking particles.
Bonding / Priming
All surfaces (except metal) – Mix 1 part super laycryl® with 1 part clean water and prime total area to be covered. As a guide, 0,1 litre of super laycryl mixed with 0,1 litre of water will prime an area of 0,75 m2.
Allow to dry for ± 30 minutes.
Metal surfaces only – Prime with 4 metal primer.
This not only gives excellent adhesion but resists rust. Allow to dry for 4 hours.
NOTE:
Do not use solvent based bituminous solutions as a primer.
Typical Physical Properties
Density (typical) | 1,18 g/cm3 |
Flash point | None |
Finish | Matt |
Fire resistance of wet film | Non-flammable |
Consistency | Soft |
Available colours | Red, grey, charcoal, burgundy, white, green and terracotta. |
Drying time @ 25 °C | Touch dry: 1 hour Hard dry: 24 hours Full cure: 7 days |
Mixing
Stir well before use.
Coverage
2,1 L/m2 for total system.
Application
First coat (all surfaces after priming) – Brush or roll on a fairly thick coat of super laycryl (1 litre/m2). Bed the membrane into the wet coat by using a roller or a stiff brush, avoiding the formation of bubbles or wrinkles. On flat surfaces it is recommended to use a fluted aluminium roller. Membrane overlaps should be a minimum of 100 mm on end laps and 75 mm on side laps.
Second coat – Once the first coat has dried sufficiently to take working traffic (2 – 3 hours depending upon weather), apply a second coat of super laycryl® (0,5 litre/m2) to ensure the membrane is completely saturated.
Third and final coat – When the second coat is dry, apply a finishing coat of super laycryl® at right angles to the second coat (0,5litre/m2).
Cleaning of Equipment
Tools, brushes and mixing equipment should be cleaned immediately after use and before material has set with abe® super brush cleaner followed by washing with soap and water.
Protection on Completion
Whilst super laycryl® is designed for an extended life, it is important to apply a maintenance coat (super laycryl) every 2 to 3 years to validate the product warrantee
Note: Do not cover with stones or stone chippings
Temperature & Relative Humidity
Do not apply super laycryl® if rain is imminent or if the temperature is below 5 °C.
Model Specification
Coloured acrylic and rubberised bitumen waterproofing flashing system plus abe® membrane.
The waterproofing/flashing system will be super laycryl®, a single-pack, elastic acrylic and rubberised bitumen compound applied in accordance with the recommendations of a.b.e.® including abe® membrane and 4 metal primer where necessary.
Packaging
1 L, 5 L, 20 L containers.
5 L kits (liquid & membrane).
Handling & Storage
This product has a shelf life of 12 months if kept in a dry cool place in the original packaging. In more extreme conditions this period might be shortened.
Health & Safety
super laycryl® is non flammable but should not be allowed contact with skin and eyes. The use of gloves and eye protection is advised. Splashes into eyes should be washed immediately with plenty of clean water and medical advice sought thereafter.
Cured super laycryl® is inert and harmless.
Important Note
This data sheet is issued as a guide to the use of the product(s) concerned. Whilst a.b.e.® endeavours to ensure that any advice, recommendation, specification or information is accurate and correct, the company cannot accept any liability for application – because a.b.e.® has no direct or continuous control over where and how a.b.e.® products are applied.
Further Information
Where other products are to be used in conjunction with this material, the relevant technical data sheets should be consulted to determine total requirements.
a.b.e.® has a wealth of technical and practical experience built up over the years in the company’s pursuit of excellence in building and construction technology.